Maybe you’ve been impressed by photos of the wide oak boards lining a friend’s kitchen only to learn they’re actually vinyl. Or have enjoyed the whitewashed planks—and easy care—of wood-look vinyl floors in a beach-house rental. This “luxury vinyl” is the fastest-growing category in flooring, and with good reason: It looks good, goes down quickly, is easy to care for, feels comfortable underfoot, and lasts a long time.
While luxury vinyl isn’t technically new, it has under- gone significant improvements. The term first appeared in the 1990s as a way to distinguish glue-down or peel-and-stick scratch-resistant tiles and planks that looked more like stone or wood, and less like the speckled stuff lining the hallways of your high school. But those early products were thin, with a floppy construction that could only be adhered to the substrate.
While that style of vinyl is still available today, “luxury vinyl” increasingly describes a product with a core and tongue-and-groove edges that enable click-and-lock installation. The first cores were made of a waterproof, wood-plastic composite that made the vinyl stiffer and able to span inconsistencies in the subfloor.
A later waterproof stone-plastic composite core makes luxury vinyl plank (LVP) and tile (LVT) flooring even stiffer and more resistant to scratches and dents. Many LVP and LVT products come in both click and glue-down formats, and every version can provide the same crisp photo-printed layer, embossed texture, range of sizes, and wear layer. Once you find the right look, the biggest decision is the installation method you choose.
Here’s the lowdown on putting the latest generation of this easy-to-live-with flooring to work in your home.
Frequently Asked Questions
How much does luxury vinyl flooring cost?
Click-and-lock LVP ranges from $1.39 to $5.99 per square foot and glue-down from $1.20 to $7.72. Expect to pay $2.49 to $5.27 per square foot for click-and-lock LVT, $1.86 to $4.84 for glue-down.
How long does luxury vinyl flooring last?
When well cared for, luxury vinyl can last up to 25 years. Most warranties range from 15 years to limited lifetime, and they can vary even within a single brand depending on the thickness of the vinyl and wear layer. Warranties generally don’t cover cuts, burns, fading, or dulling from normal wear and tear.
Where to buy it?
LVP and LVT are sold at home centers and independent flooring stores; the latter tend to offer more and higher-end options.
DIY or hire a pro?
A click-and-lock vinyl floating floor is a popular DIY project. Consider gluing down a floor if you’re comfortable laying tile. Pro installation adds $3
to $10 per square foot.
Luxury vinyl flooring maintenance
Clean up acidic spills like tomato sauce promptly to prevent staining. Remove debris by sweeping, vacuuming (no beater bar), or dry mopping with a neutral pH cleaner to avoid abrasion; add felt pads to furniture feet. Some brands offer a liquid polish to restore a worn vinyl floor’s luster.
Pros and Cons of Luxury Vinyl Flooring
While LVP and LVT can be easier-on-the-wallet alternatives to real wood and ceramic or stone tile, and improved looks give them a goes-anywhere-in-the-home reputation, the material still has some limitations.
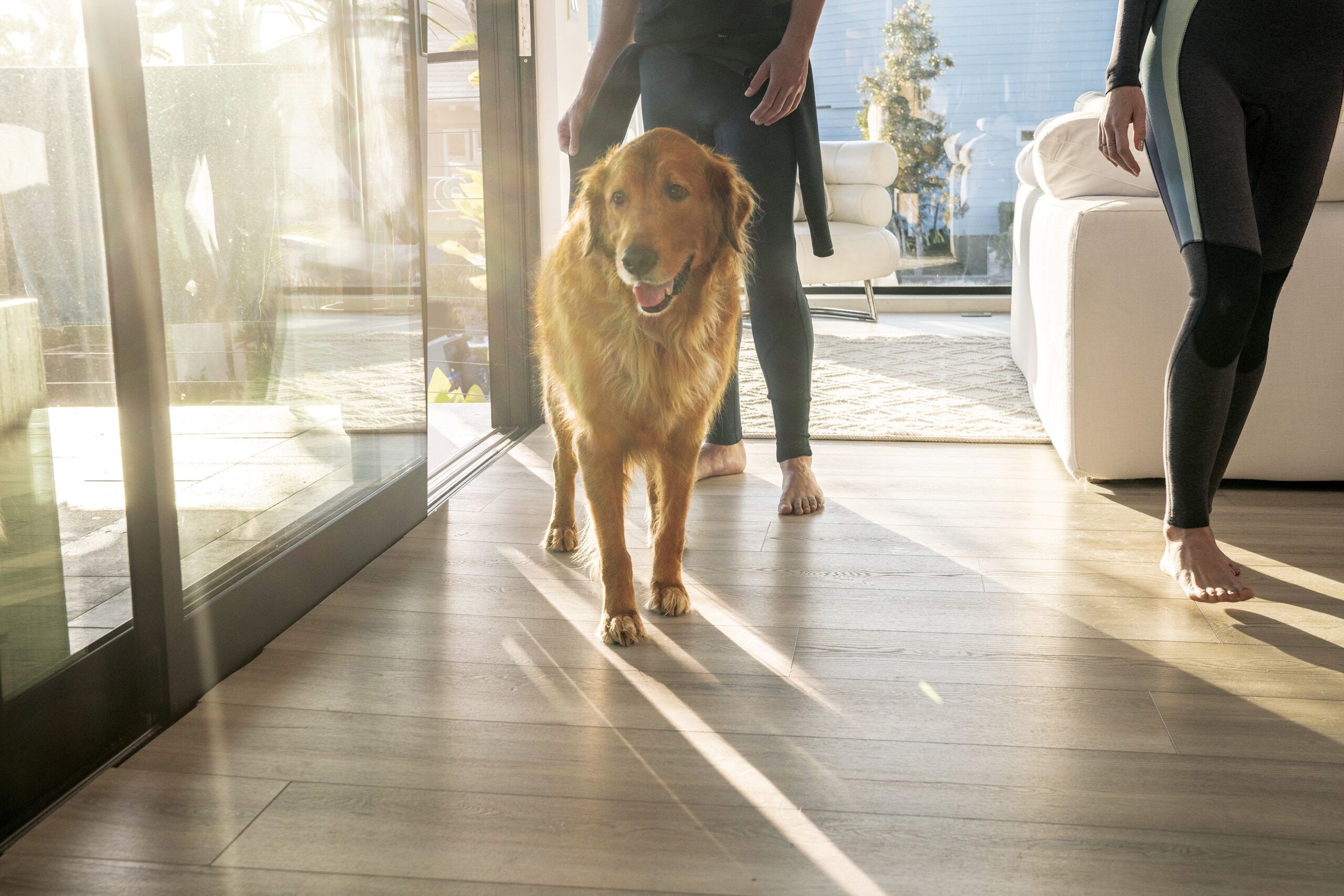
Pros
- Realistic looks: Manufacturers have made huge strides in replicating the look of wood flooring, with improved high-definition photo-printed imagery, as well as edges milled with micro-bevels that mimic those found on pre-finished hardwood. Some stone- look tiles can even be finished with grout.
- Resilient underfoot: Luxury vinyl offers some slight give underfoot, so it can be more comfortable to stand on long-term than wood or stone. This resiliency, by way of padding, means the floor is also quieter to walk on, a bonus in upstairs rooms.
- Low maintenance: Because the flooring is waterproof, it cleans up easily, and its tough polyurethane wear layer resists normal scratching, including from pets’ nails.
- Can be DIY-friendly: Click-and-lock flooring outsells glue-down options due to ease of installation. If you’ve installed tongue- and-groove flooring before and are willing to pay attention to the surface preparation—like feathering the grout joints of an existing tile floor—you can install luxury vinyl without ripping up the existing substrate.
- Can be less expensive: Compared with pre-finished hardwood flooring and real stone tile, luxury vinyl can be more affordable. But the major savings are in professional installation, especially where labor costs are high, if you’re able to lay it yourself.
- Design flexibility: You can find wood-look planks up to 12 inches wide and 96 inches long, sizes that would be out of reach in hardwood, and in finishes that are pricey to replicate on-site, including liming and whitewashing. Herringbone, basket-weave, and parquet designs are now options, as is the ability to cover a staircase in the same material. Diamond and hexagon shapes enable patterned tile floors, as do printed designs that suggest marble or cement tile.
Cons
- Can still scratch or be cut: While luxury vinyl is durable, a dropped chef’s knife can cut it, a hot pot can melt it, and, while scratch resistance has improved, furniture dragged on it can scuff the finish.
- Can’t be refinished or repaired: Unlike wood flooring, you can’t refinish vinyl, though you may be able to bring back its luster. Replacing a damaged click-and-lock plank is relatively easy, but doing the same with a glued-down tile can be a headache.
- Can fade: Vinyl is susceptible to discoloration when exposed to direct sun, even in flooring that includes a UV inhibitor. This fading is not usually covered by warranty.
- May not be radiant compatible: While it doesn’t have the mass of tile, luxury vinyl’s thinner body can still transfer radiant heat. But not all manufacturers approve their products for use with radiant due to the potential for expansion and color degradation. If it is compatible, the underfloor heat setting will likely have to be kept below 80 degrees F.
- Likely won’t add to resale value: While luxury vinyl tile can offer the look of hardwood, stone, or ceramic tile flooring, it usually doesn’t increase resale value the way those flooring materials can.
Getting to the Core
Understanding a couple of acronyms can help guide you to the best product for your project.
WPC (Wood Plastic Composite) Core
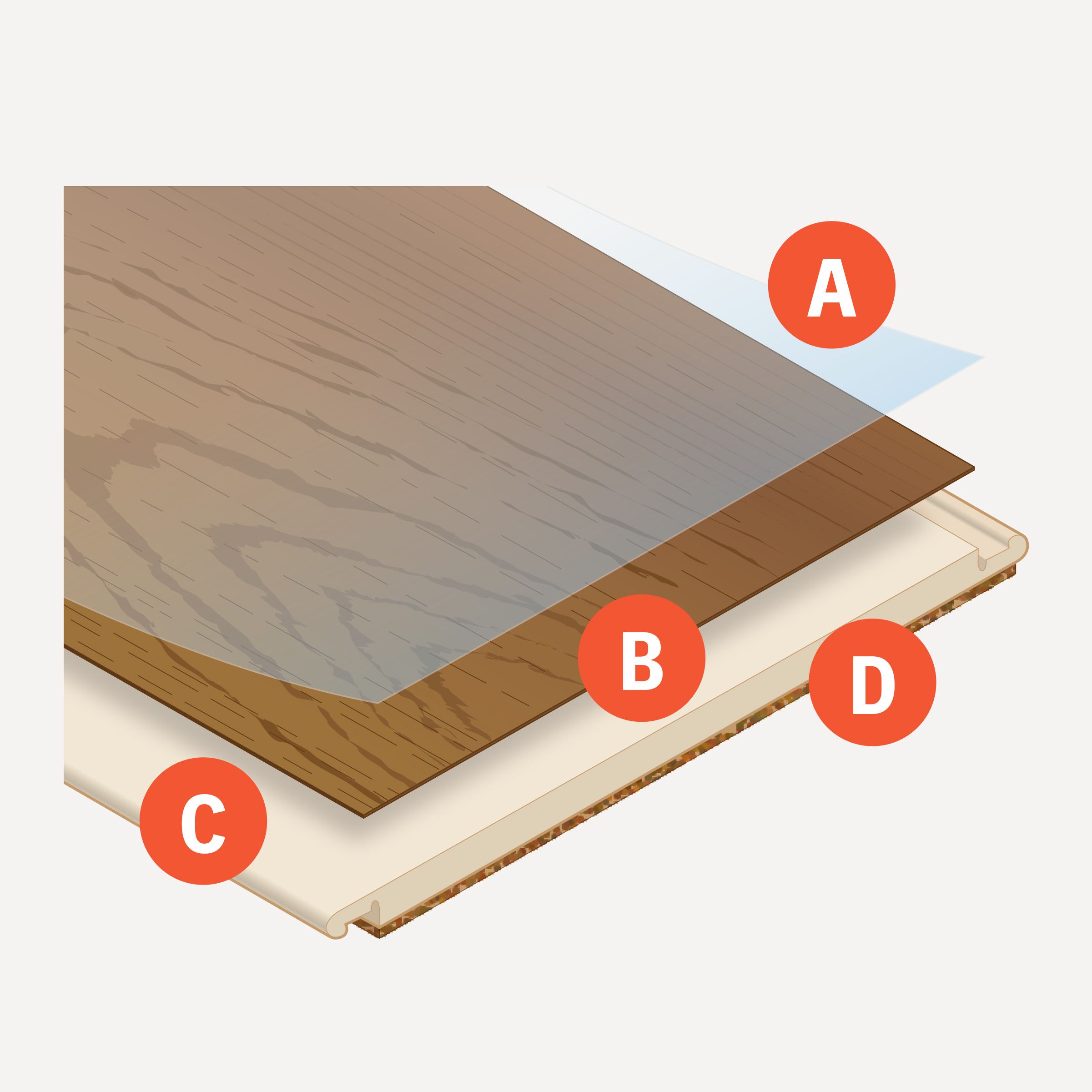
WPC is the first rigid luxury vinyl plank, designed to compete with tongue-and-groove, pre-finished hardwood floors. A top wear layer of polyurethane (A), measured in mils (the equivalent of one- thousandth of an inch), covers a photo-printed layer that offers a realistic wood or stone look (B). The core (C) is typically made of polyvinyl chloride (PVC), calcium carbonate, plasticizers, and a foaming agent. The tongue- and-groove edges (and a textile stability layer, if present) are part of the core. Last, a backing, or underlayment (D), often cork, adds softness underfoot and helps dampen sound transmission. While adding a WPC core made luxury vinyl floors more DIY-friendly, the knock against them is they can dent under very heavy furniture.
SPC (Stone Polymer Composite) Core
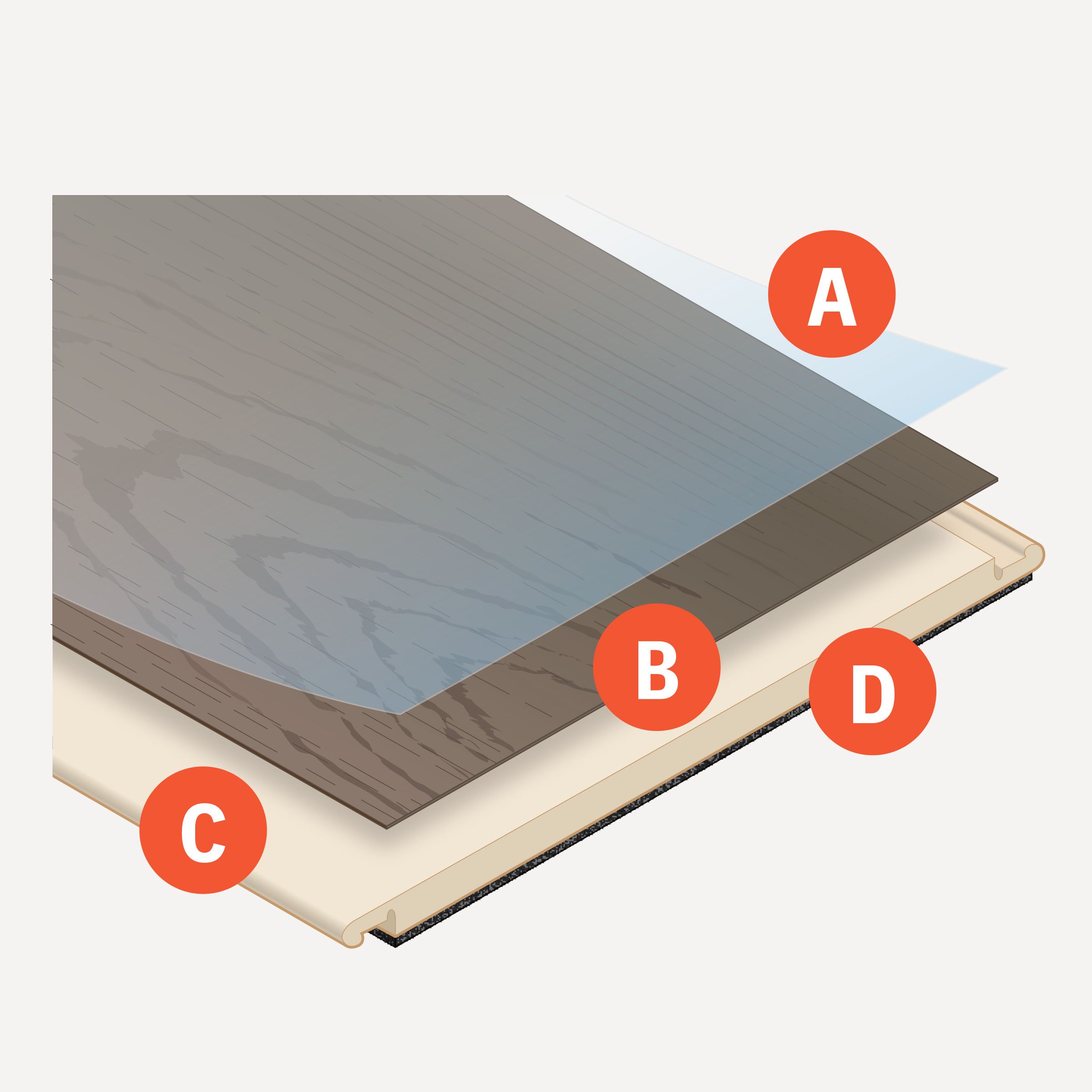
Introduced in 2017, SPC luxury vinyl brings back some of the limestone found in old-school vinyl composition tile to replace the wood in WPC. The result is a stiffer, stronger, and heavier waterproof plank that is more dimensionally stable. Like WPC, SPC planks start with a polyurethane wear layer (A) protecting a decorative image layer of wood or stone (B). The core (C) is a mixture of limestone, PVC, and stabilizers, and includes the plank’s tongue-and-groove edges. The underlayment (D), often foam, makes the planks quieter. While not as quiet or as soft underfoot as WPC, today’s SPC is more dent and scratch resistant. Dimensionally stable, SPC floors can withstand the temperature and humidity swings of a three- season room.
Durability Counts
A thick wear layer is one mark of quality. Here are three vinyl flooring options with varying durability.
Good
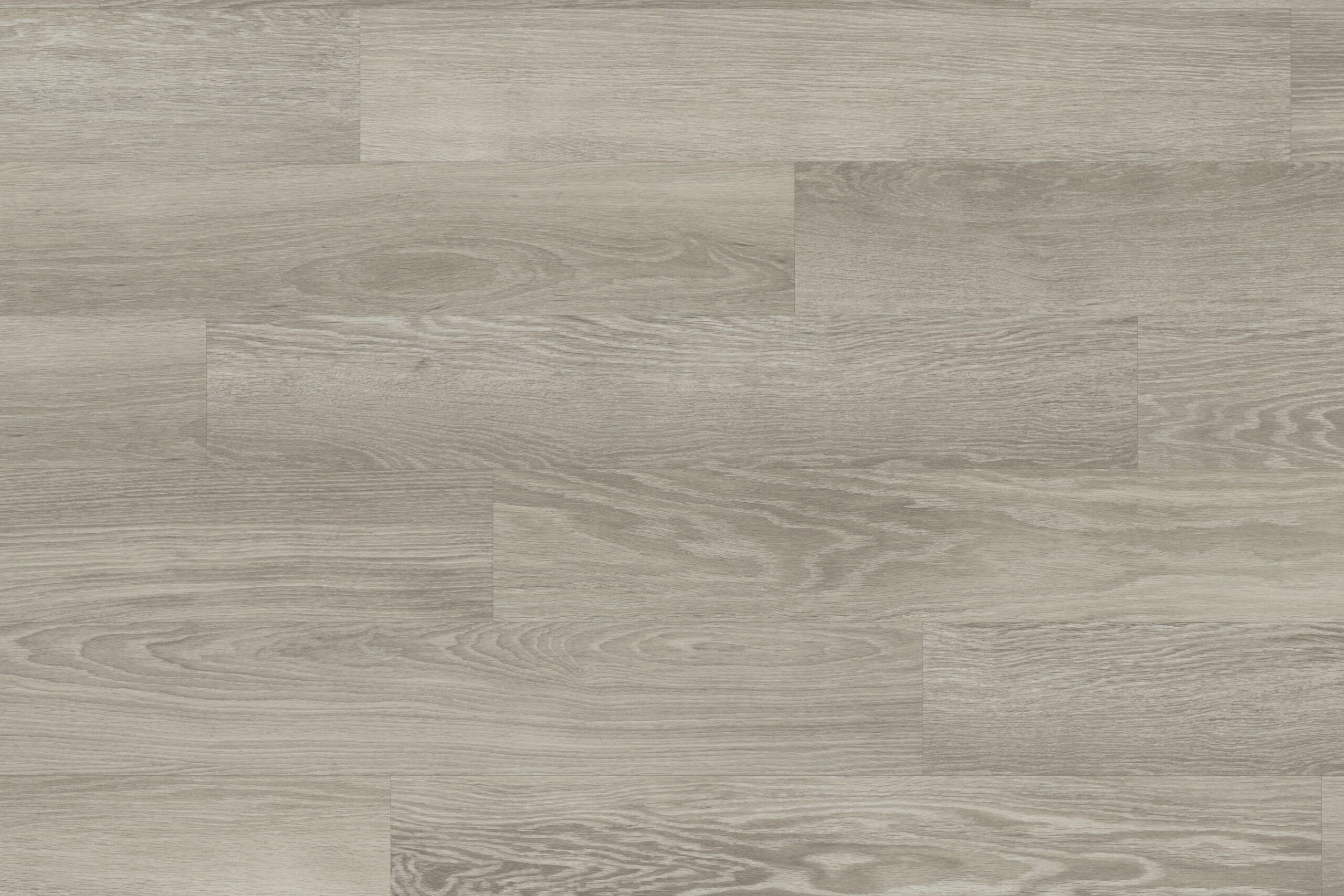
Knight Tile in Grey Limed Oak SCB-KP138-6
- The look: Oak graining with a gray-washed finish
- Details: Click-and-lock planks, SPC core; 36×6 inches and 2mm thick; 12-mil wear layer
- Cost: $4.58 per sq. ft. uninstalled; karndean.com
Better
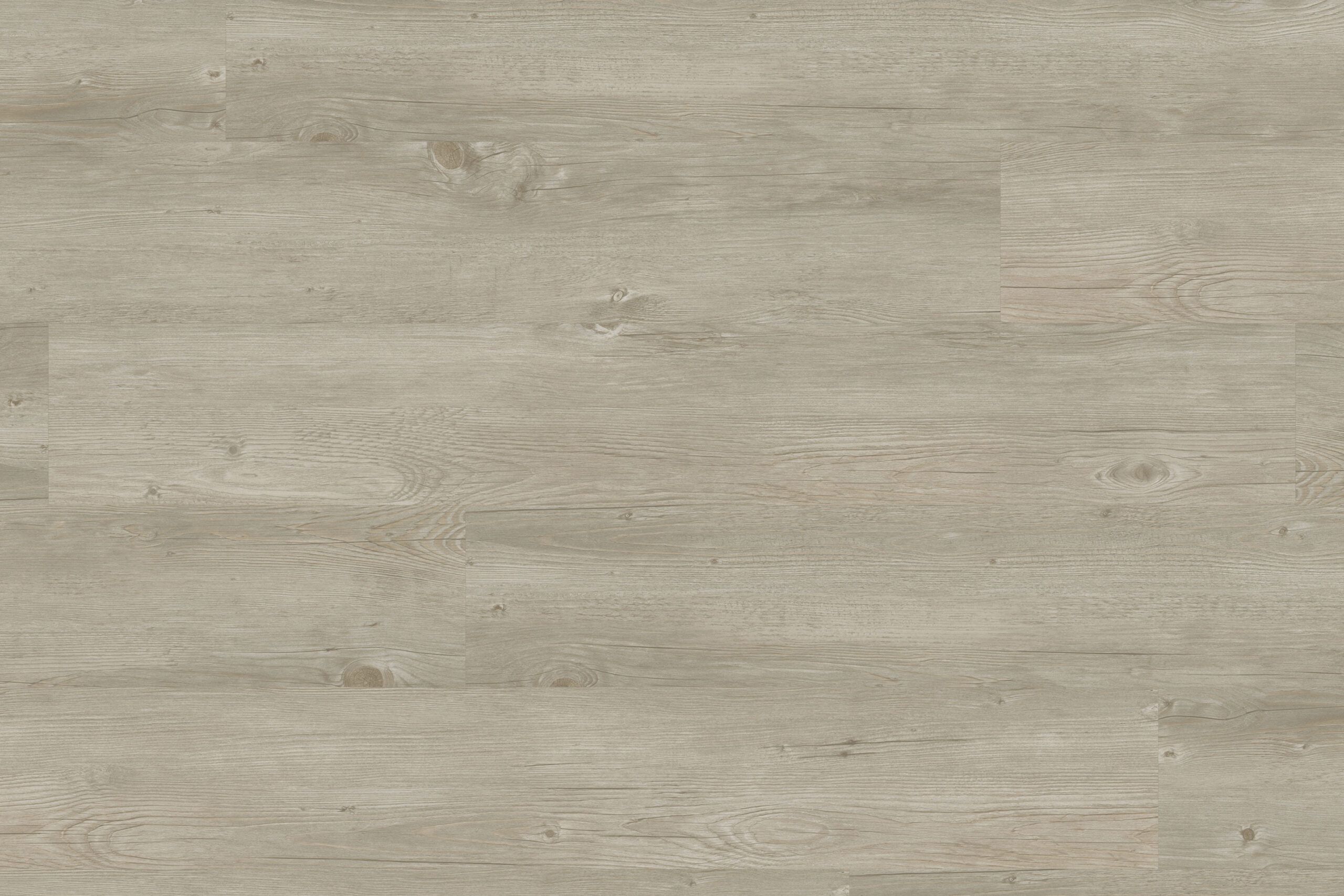
Van Gogh in Light Country Oak SCB139
- The look: Longer pale oak planks with graining, more knots, and deeper embossing
- Details: Click-and-lock planks, SPC core; 48×7 inches and 41/2mm thick; 20-mil wear layer
- Cost: $5.08 per sq. ft. uninstalled; karndean.com
Best
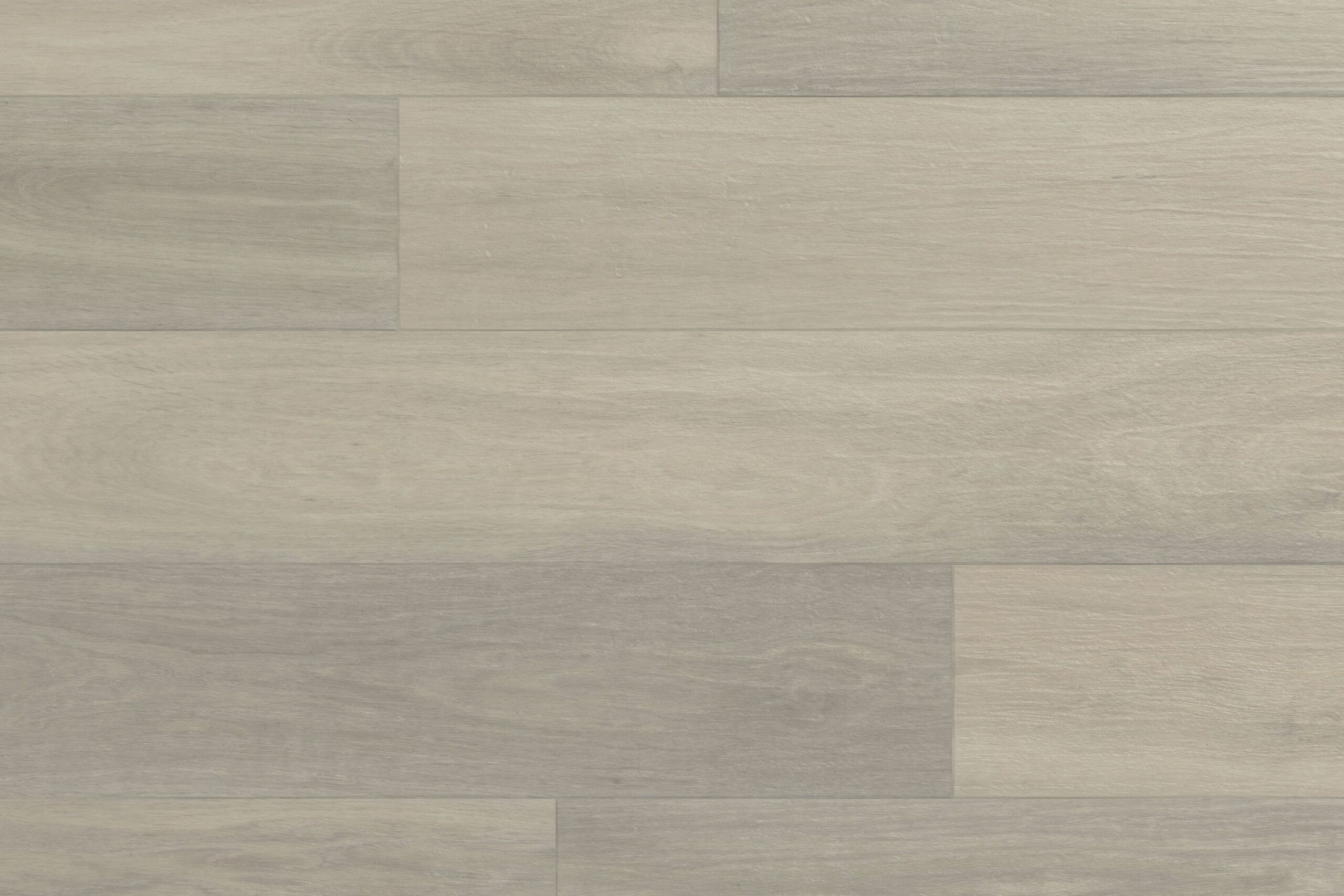
Art Select in Glacier Oak RL21
- The look: Larger planks with the refined graining, hand-scraped texture, and matte finish of French oak
- Details: Glue-down planks (click-and-lock coming in May); 56×9 inches and 3mm thick; 30-mil wear layer
- Cost: $6.87 per sq. ft. uninstalled; karndean.com
Ways to Install Vinyl Flooring
DIY it or hire a pro—either way, there are factors to consider when deciding which method is best for your project.
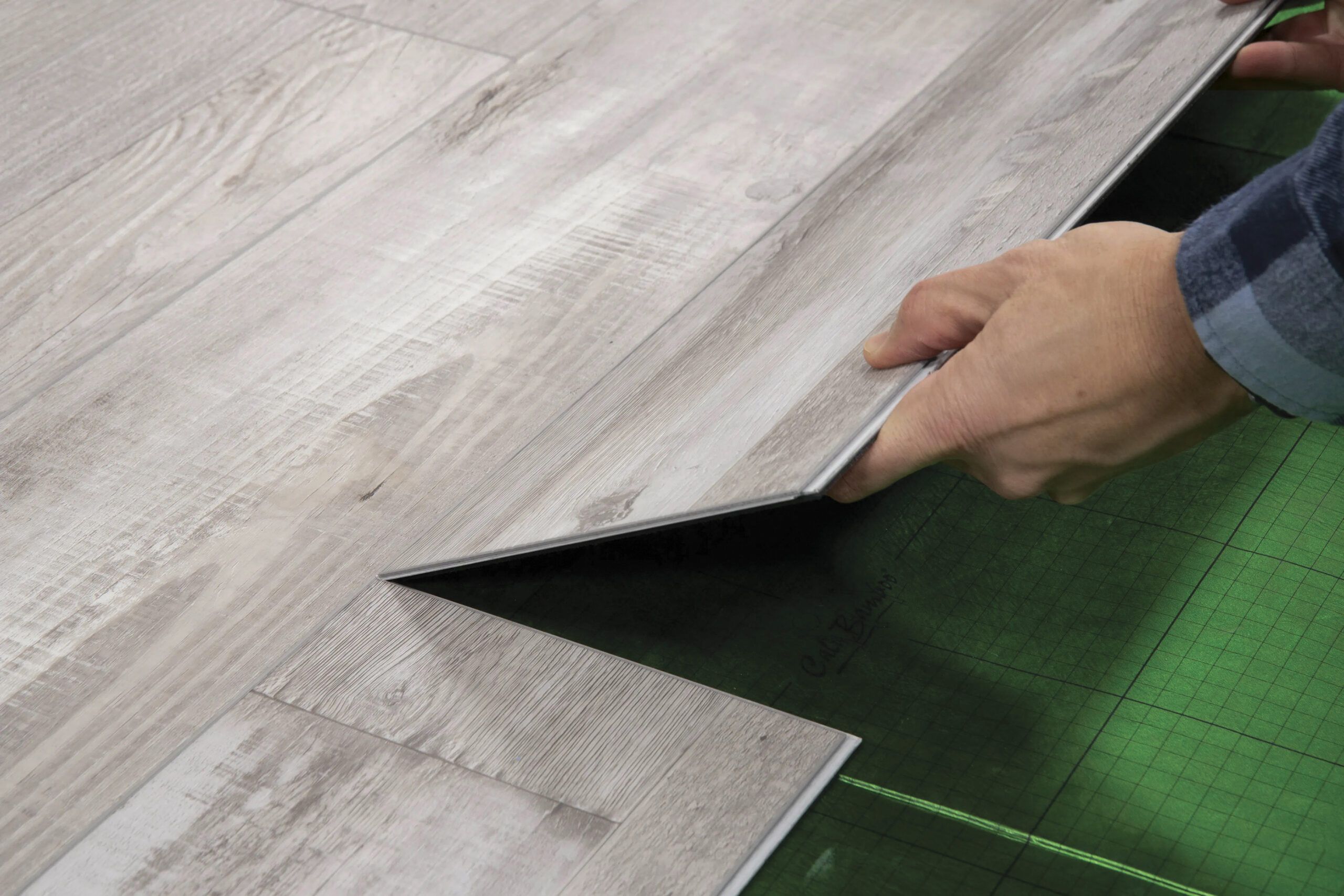
Click-and-lock (a.k.a. floating)
Similar to the tongue-and-groove system on wood floors, click-and-lock flooring holds together as one monolithic mass that floats over the subfloor. It’s faster to install than glue-down types, and more popular. Other things to keep in mind:
- It generally needs to acclimate. Like wood, click-and-lock flooring might need to acclimate to ambient temperatures for a few days prior to installation. Once that’s done, however, the vinyl can float over just about any first-floor or upstairs room in the house.
- Mind the expansion gap. Pro installers typically run any grain pattern in line with the longest dimension in the room, leaving a gap around the floor perimeter of about 3⁄4 inch to allow for expansion and contraction.
- The substrate is key. An underlayment is not generally needed when installing LVP or LVT over a plywood subfloor. However, a vapor barrier is recommended when installing directly over concrete. If the existing concrete floor is not flat, or slopes or dips more than 1/8 inch over 4 feet, patch it with leveling compound before installing vinyl plank or tile.
- Water can be a problem. While the flooring itself is waterproof, a flood can trap moisture between the vinyl and the substrate, which is why warranties usually don’t cover flood damage that might lead to rot or mold.
Glue down (a.k.a. dry back)
Installing vinyl over troweled-on glue is more time-consuming, but it can be the better option, especially over a concrete basement floor, where flooding from rain or a burst laundry-supply line won’t reach the substrate. Other things to keep in mind:
- There is added cost. With glue-down flooring you’ll also need to purchase the adhesive, which runs about $50 for a low-odor formulation sized to cover up to 260 square feet, along with the trowel to spread it.
- The substrate is still key. While you can glue down rigid luxury vinyl, most dry-back installations use uncored, all-vinyl planks and tiles, which telegraph inconsistencies in the substrate like high and low spots. These don’t just look bad; high spots can also wear out sooner.
- There’s a timeline. The adhesive used for a glue-down floor has an open working time between 20 and 40 minutes, so if you DIY, you will want to avoid spreading more glue than you can tile over.
- Grout can add a realistic look. Some manufacturers offer glue-down luxury vinyl tile that leaves room for a grout line, for a better facsimile of stone or ceramic. During installation, you space the tiles 1/16 to 1/4 inch apart, then fill the joint with premixed sanded grout for a true tile look.
Luxury Vinyl Flooring Design Ideas
Luxury vinyl can replicate everything from patterned oak floors to high-end stone and ceramic tile.
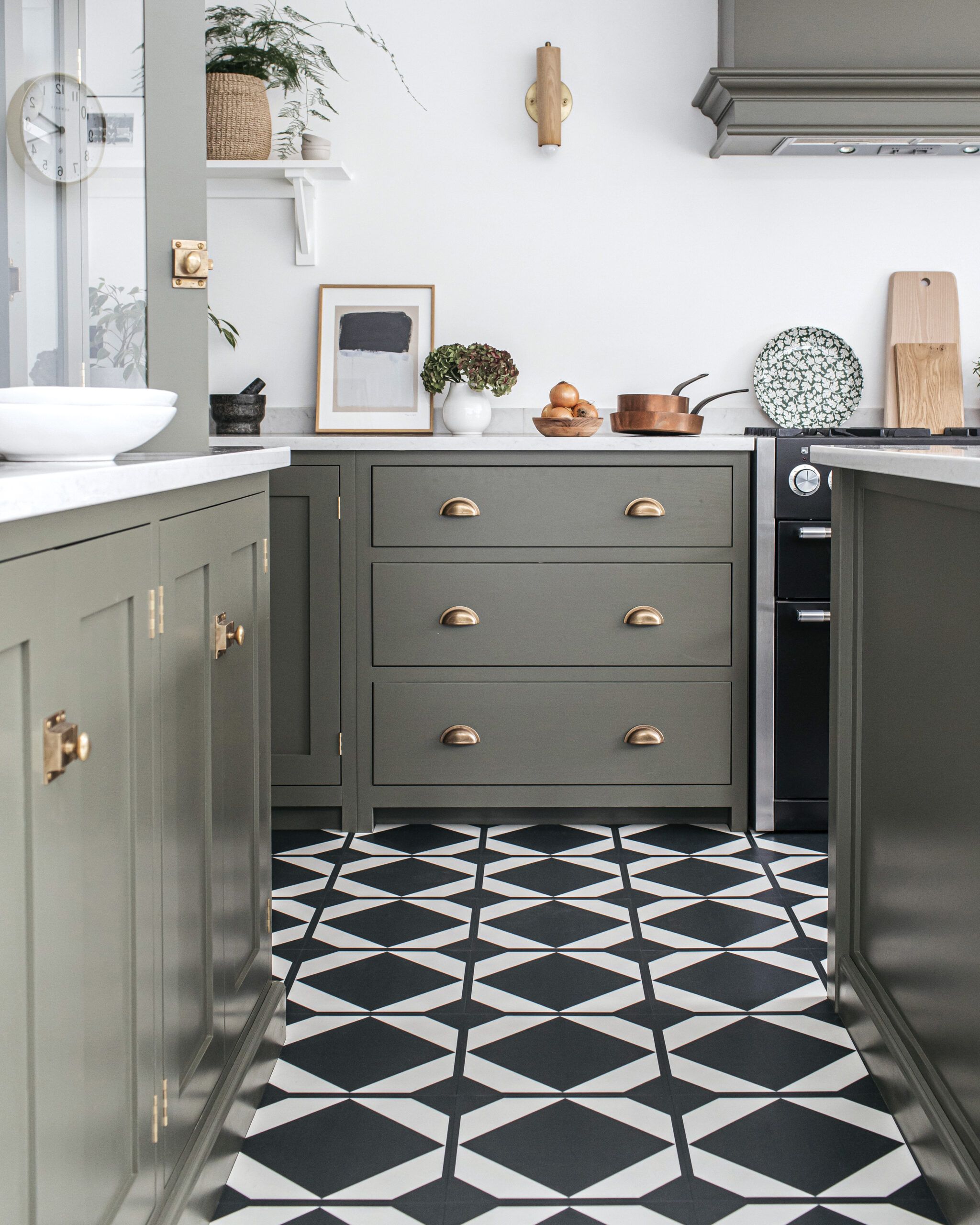
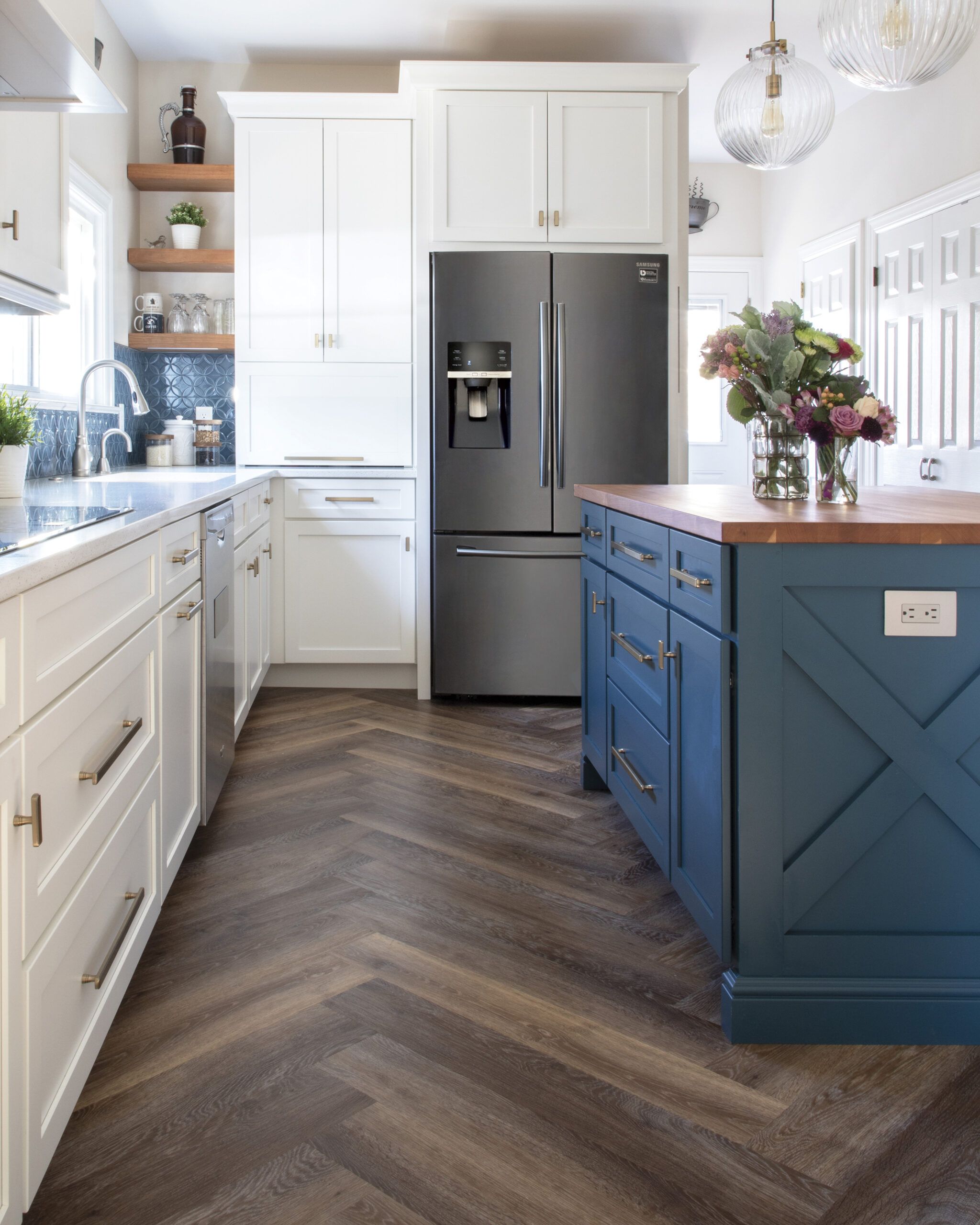
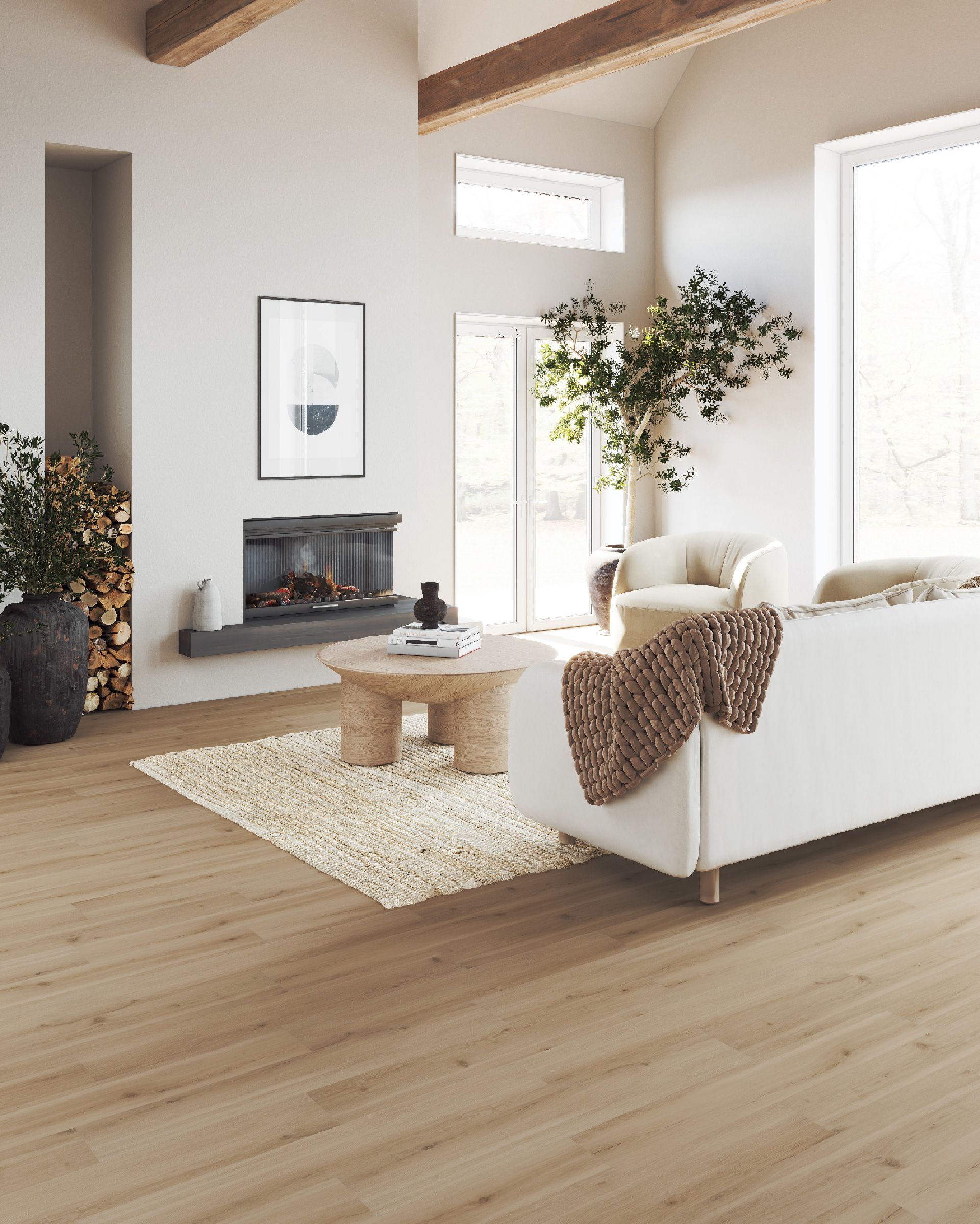
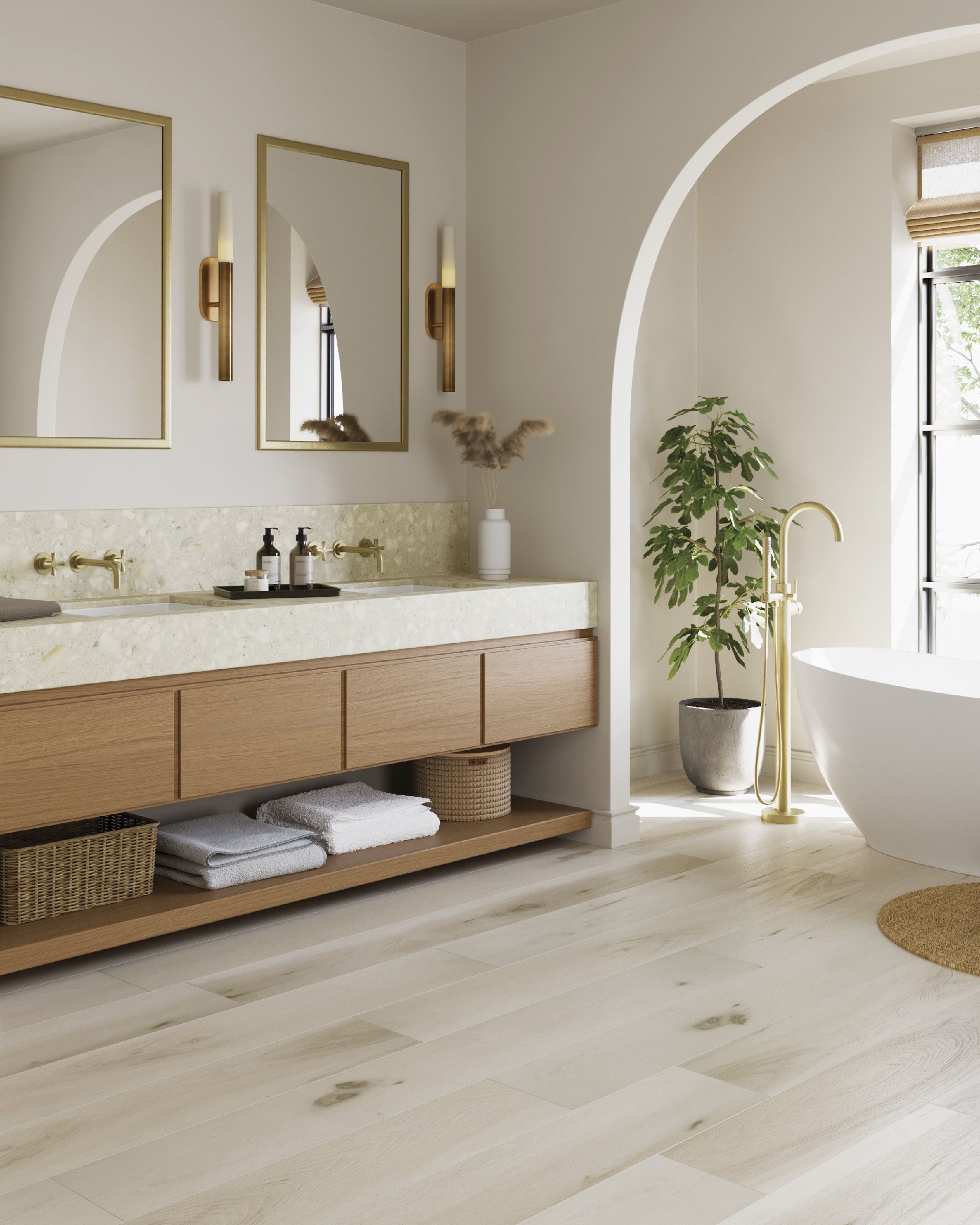
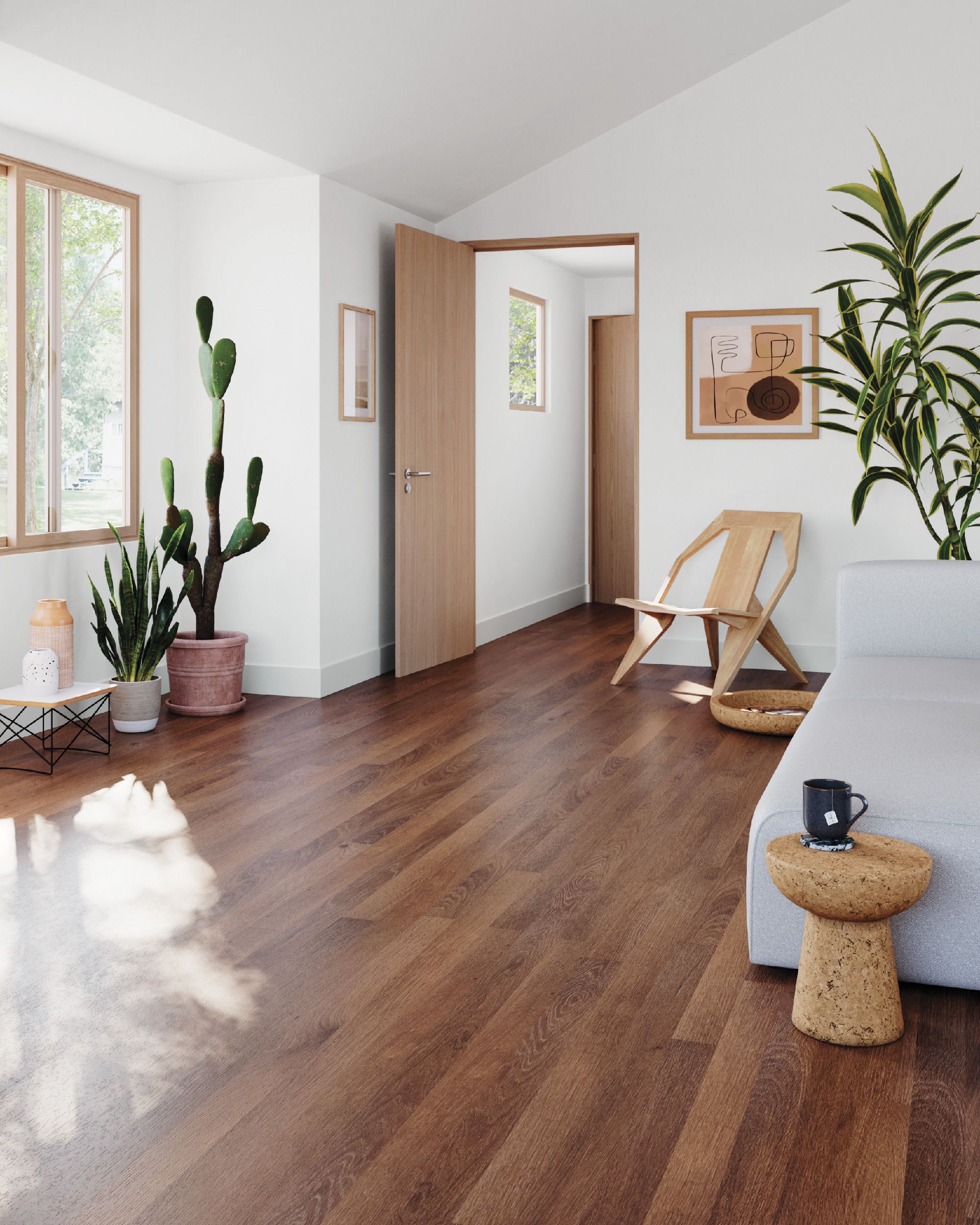
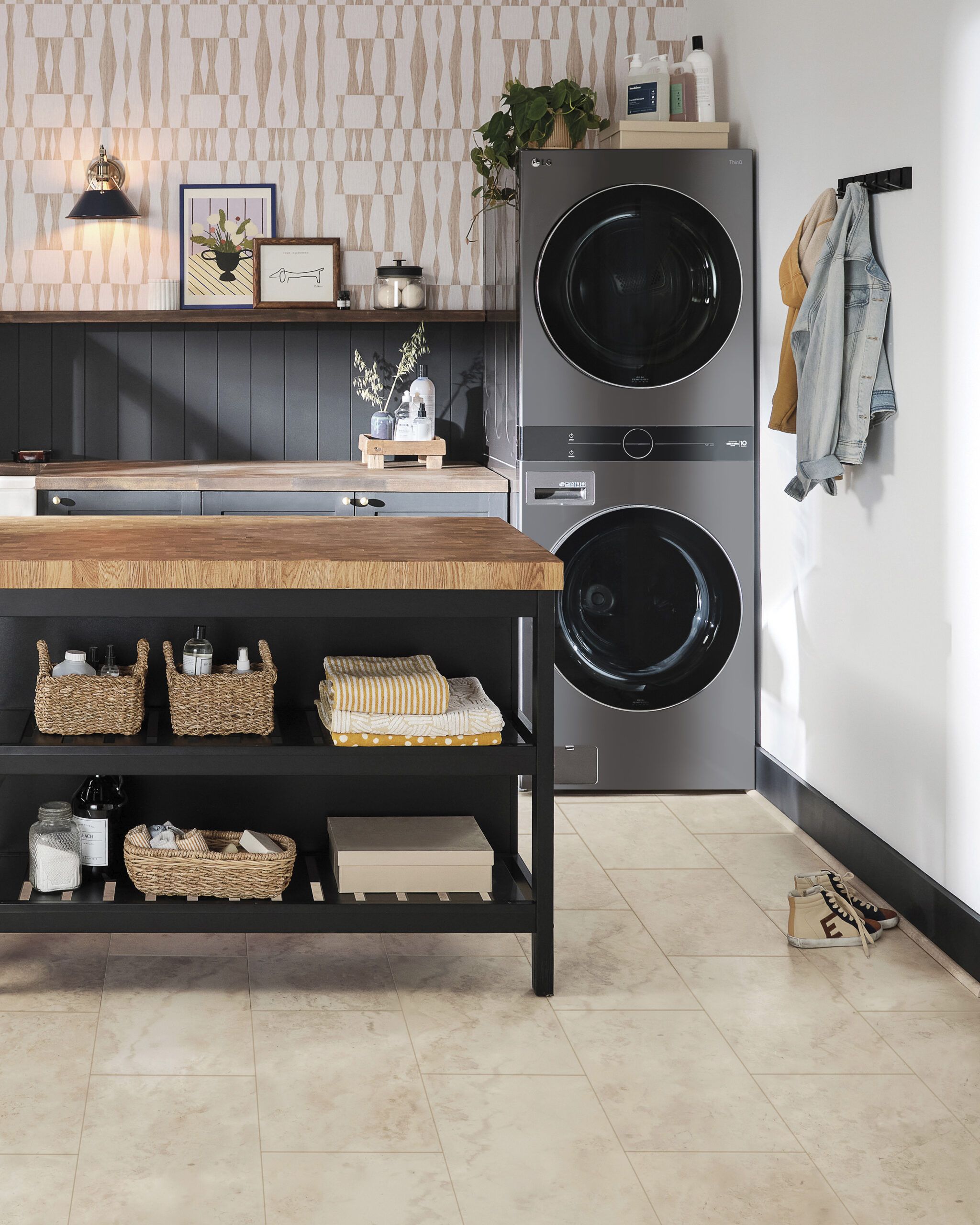
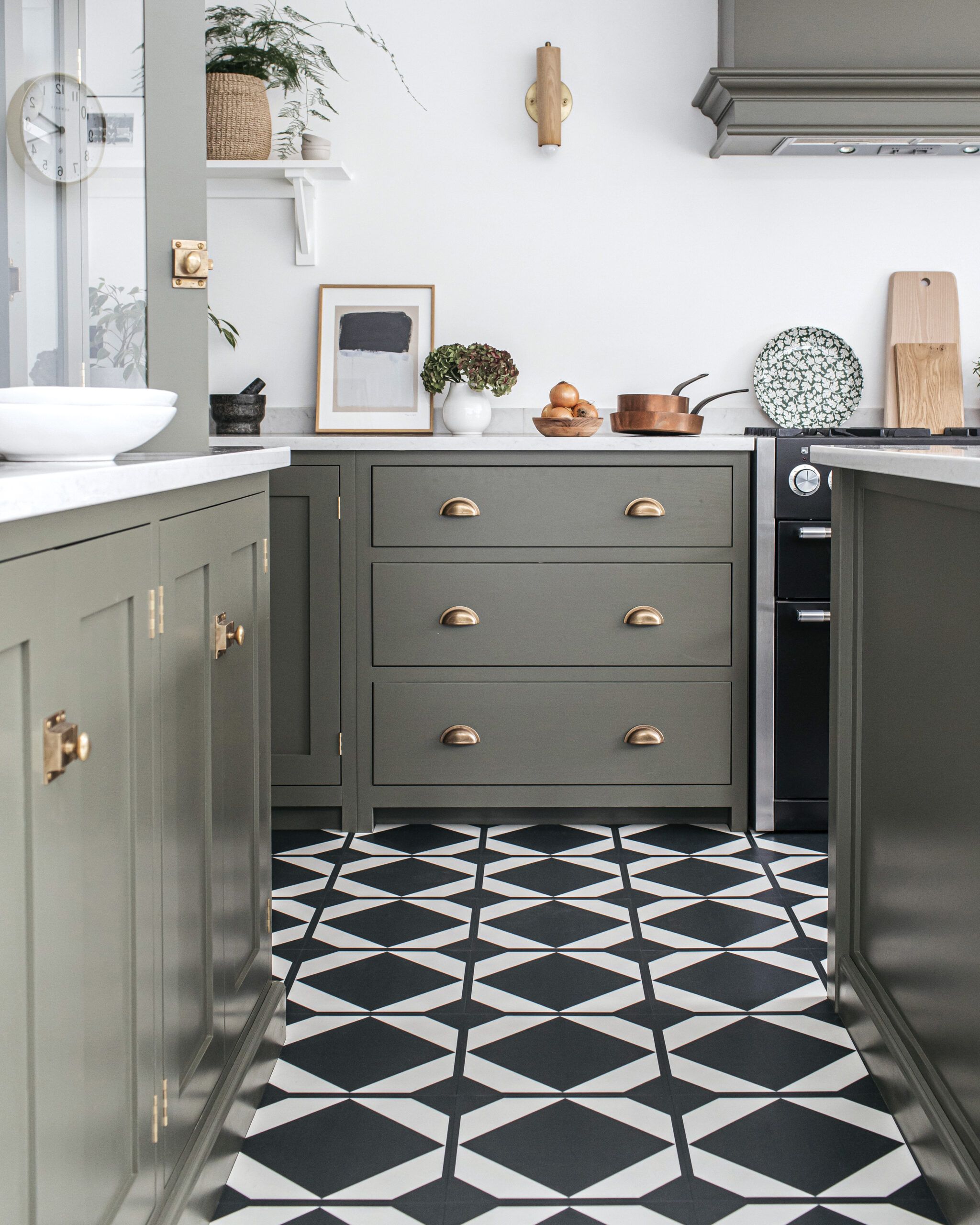
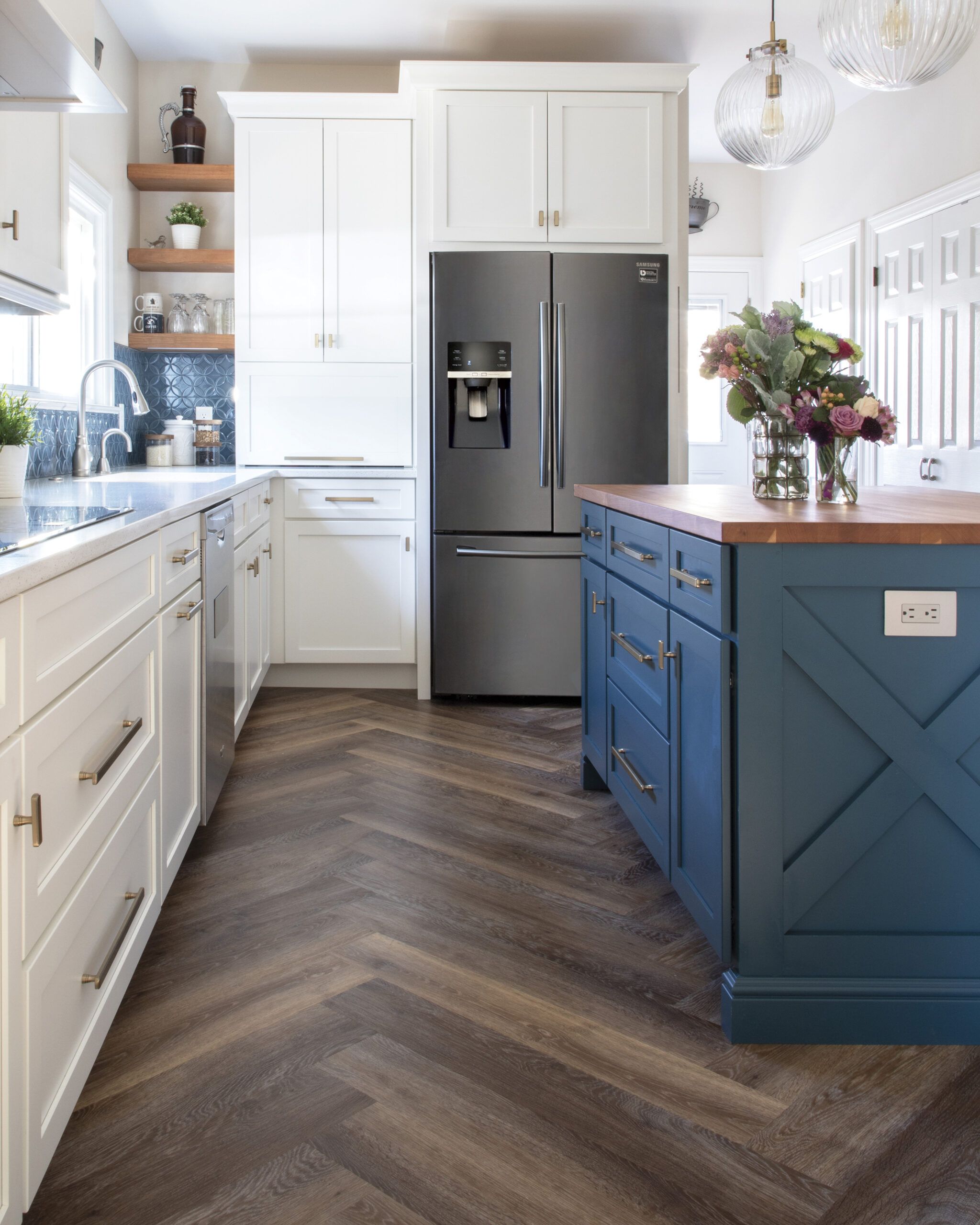
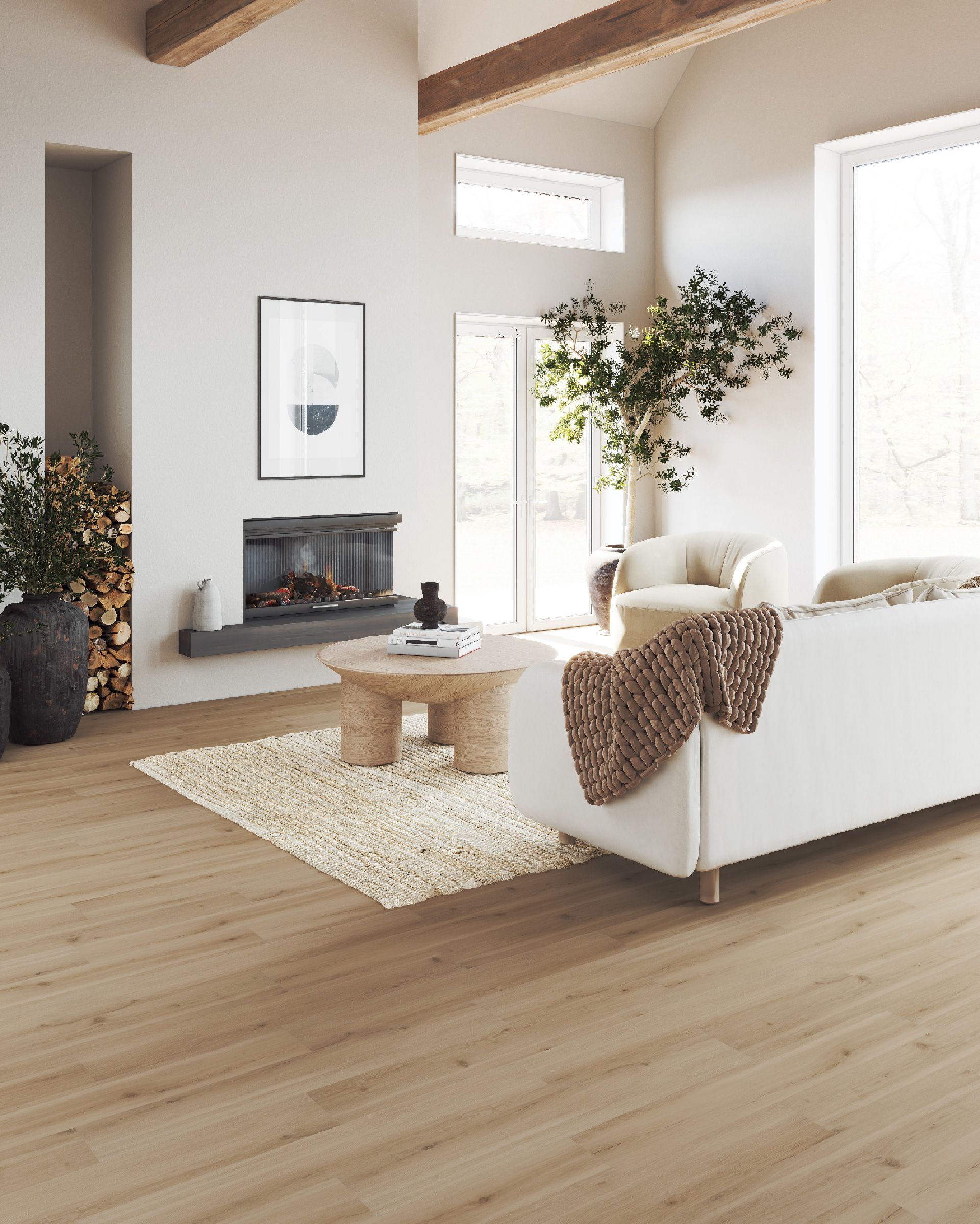
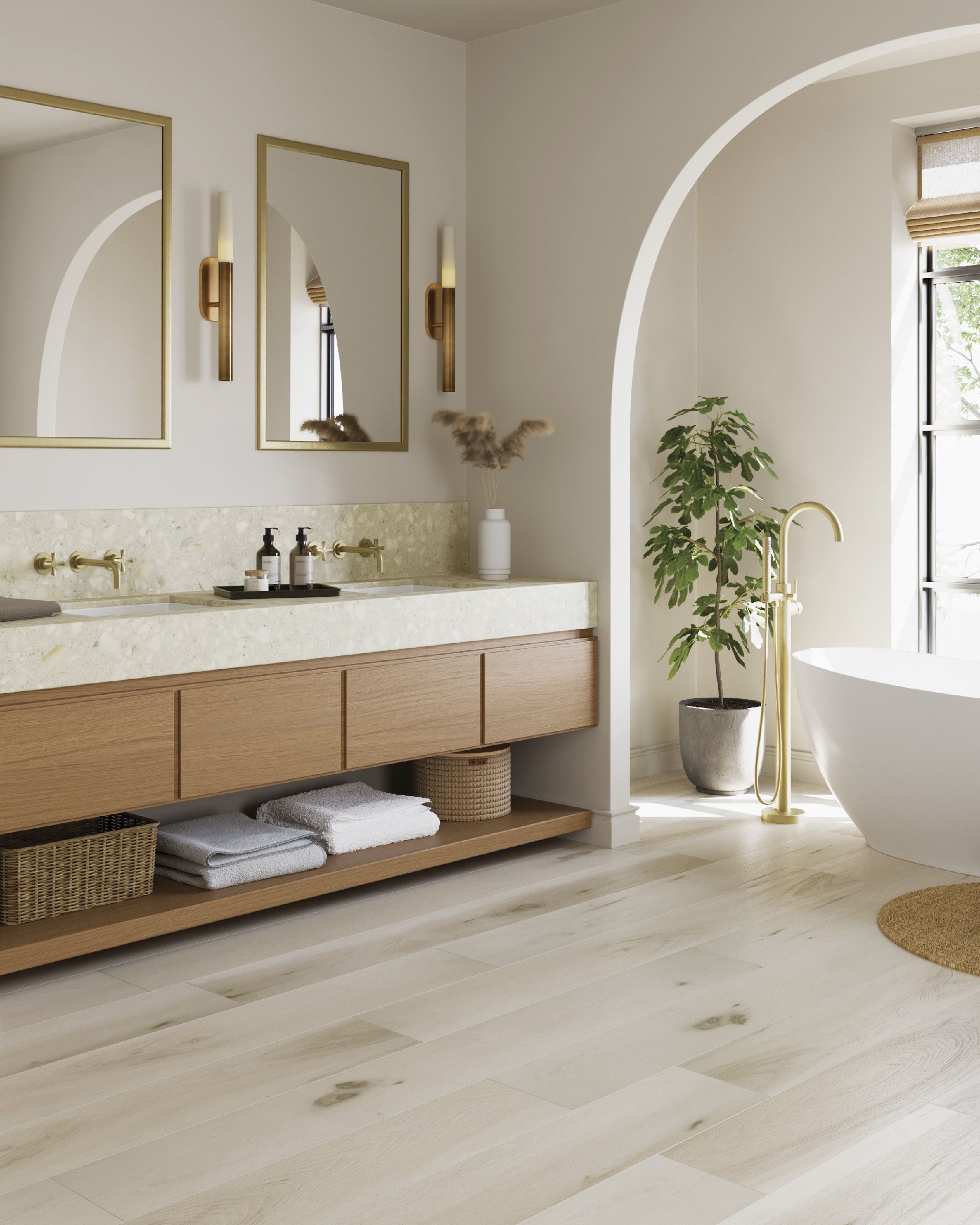
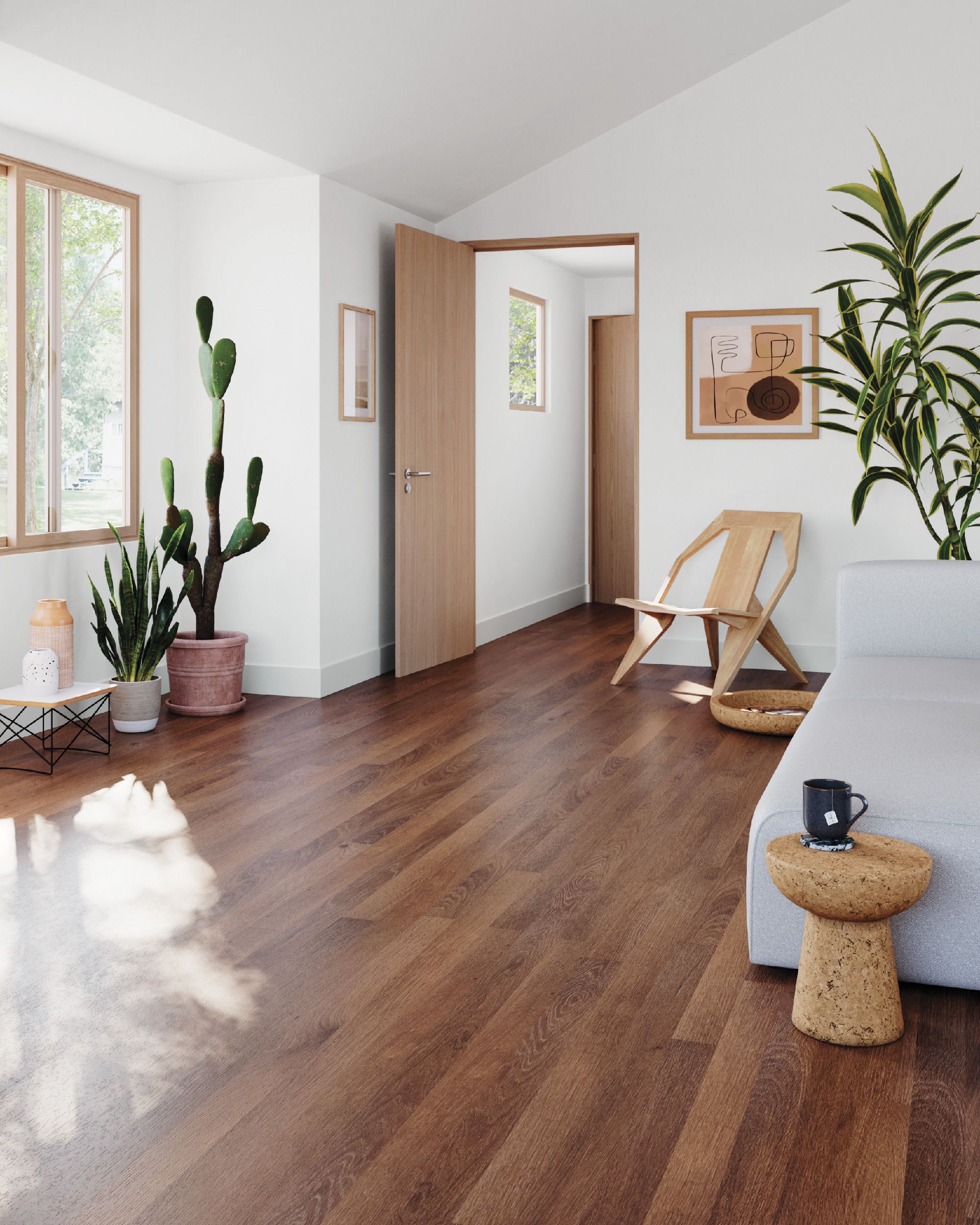
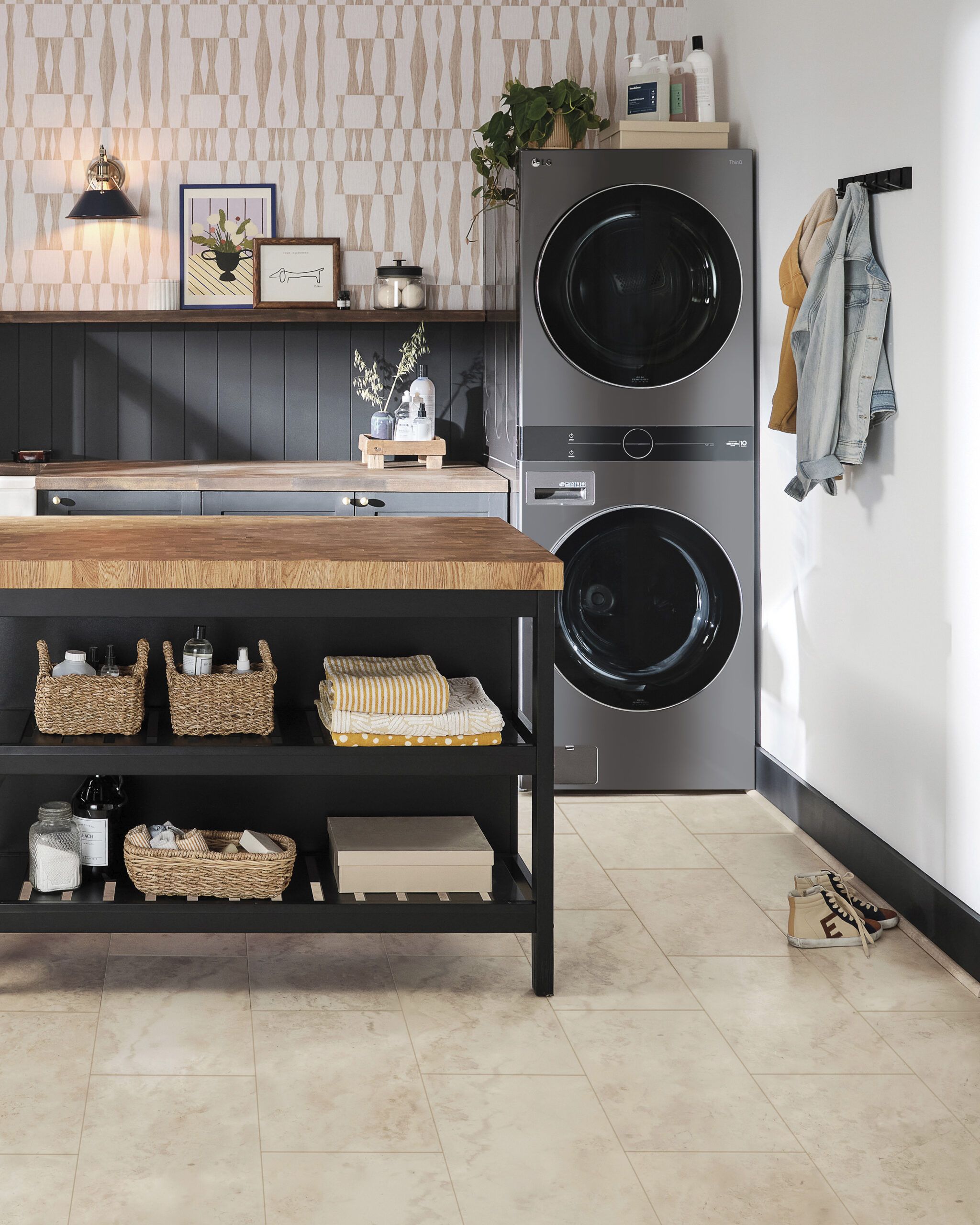